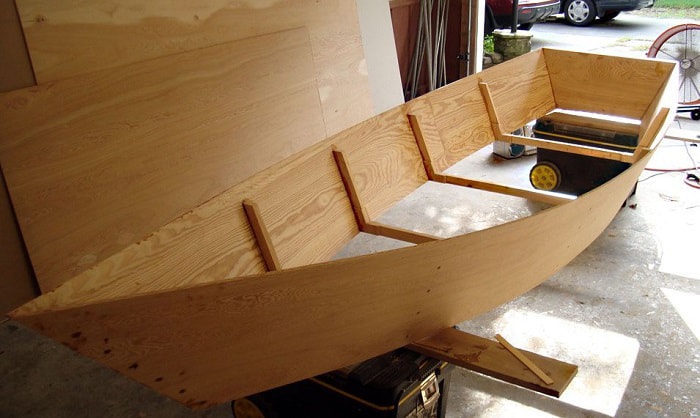
Beyond the Basics: Unlocking Plywood Boat Building Potential
Plywood boatbuilding, a time-honored tradition, often relies on established techniques. But what if we looked beyond the familiar, exploring unconventional approaches to maximize strength and stability? This article delves into lesser-known strategies and innovative thinking, offering fresh perspectives for both seasoned builders and enthusiastic newcomers.
Q&A: Unconventional Approaches to Plywood Boat Construction
Beyond the Standard Epoxy: Exploring Alternative Resin Systems
Q: Epoxy is the standard, but are there more sustainable or cost-effective alternatives for bonding plywood in boat construction?
A: Absolutely! While epoxy reigns supreme due to its strength and water resistance, research into bio-based resins is rapidly advancing. Some studies (e.g., research published in the Journal of Composite Materials) explore the use of polyurethane and even certain modified plant-based resins. These alternatives might offer comparable strength in certain applications, while reducing the environmental impact associated with epoxy production. However, thorough testing and understanding of their long-term durability in marine environments are crucial before widespread adoption. Cost-effectiveness depends heavily on scale and sourcing.
Strategic Plywood Selection: Grain Orientation and Beyond
Q: We always hear about grain orientation. Are there other less-discussed factors in plywood selection that significantly influence hull strength?
A: The type of wood veneer itself plays a huge role. While marine-grade plywood is essential, focusing solely on the exterior veneer is limiting. Consider the core layers. Harder core veneers, like Okoumé combined with a strong exterior layer, can provide superior stiffness and impact resistance compared to all-Okoumé ply. Furthermore, the manufacturing process of the plywood influences its properties. Plywood with a higher degree of lamination pressure will exhibit improved strength and water resistance.
Reinforcement Strategies: Thinking Outside the Fiberglass
Q: Fiberglass is common for reinforcement, but what are some less conventional, yet equally effective, options?
A: Natural fibers are gaining traction. Research from institutions like the University of Maineâs Advanced Structures and Composites Center shows promising results with basalt or flax fibers embedded within the epoxy matrix. These provide good strength-to-weight ratios and are more environmentally friendly than fiberglass. Another option, less discussed but effective in specific areas, is the strategic use of strategically placed hardwood stringers or ribs for added localized strength. This method is especially helpful for areas subjected to high stress, like the keel or stem.
Case Study: A Small Boat, Big Innovation
A recent project by a group of amateur boat builders showcased a remarkable approach. They experimented with using a combination of vacuum bagging and computer-aided design (CAD) to create a lightweight, exceptionally strong hull. By carefully optimizing the ply layers and reinforcement placement based on their CAD model's stress analysis, they achieved a boat with higher strength-to-weight ratio than traditional methods permitted.
This demonstrates the power of combining established techniques with modern design and manufacturing tools. Using CAD software to simulate stress points before building can significantly reduce wasted material and improve the structural integrity of the finished product.
The Future of Plywood Boat Building
The field of plywood boatbuilding is ripe for innovation. By embracing new materials, design tools, and construction techniques, we can build boats that are stronger, lighter, more sustainable, and more affordable. This requires a commitment to experimentation, collaboration, and a willingness to challenge conventional wisdom. The future of this craft lies in pushing boundaries and exploring the untapped potential of plywood as a boatbuilding material.
Further Research: Explore online forums dedicated to boatbuilding, seek out publications from materials science journals, and network with other builders to stay abreast of the latest advancements and share experiences.